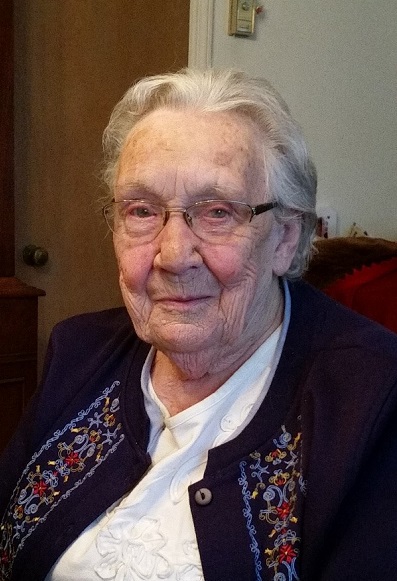
By Lucille LaTulip Johanson
I had just graduated from high school in Cloquet, Minnesota in June of 1942, and in July I had a chance to go to visit my sister in Chicago who was a nurse in a local hospital. I left for my visit on July 5, 1942. When I arrived, her husband, an Aeronautical Engineer who worked at an aircraft plant there, asked me if I was interested in working at his place of work. They were just opening up the plant to women, as the men were being called into service.
It didn’t take me long to think about it, and I decided I’d stay in Chicago and check it out. The Pullman Railroad Car Seat factory had been converted into an aircraft plant and was now making wings, ailerons, nose pieces, spars, and etc. for the C-47 transport airplanes. We called these parts appendages. These assemblages were then shipped to the California based plant for final assembly of the aircraft.
I was accepted for a 6 week course at a trade school, where I received a graduation certificate making me qualified for a job at Pullman Aircraft. I still have my practice rivet plate, note book, and safety glasses which were used in a display for “Rosie the Riveter” at our local Historical Society. Who would have thought they would have been important to anyone else but me?
When we arrived each morning, the men went in one line to be checked out by a man who saw to it that they weren’t carrying in anything banned from the work place. We women went in a different line where our purses were checked and our slack legs were checked also, but by a woman. The first ten women were sent to the Sheet Metal area to begin learning from the bottom up. We then went to another shop where we picked up the tools, drills and other items e needed for working at an upright drill press machine on sheets of metal. As women working in a “man’s” world, we had to take a lot of teasing and harassing especially when acquiring these parts. We had to take on a “I Can Do It!” attitude as we would now be the first women to be working in the plant other than a nurse and a few secretaries.
We worked 8 hour shifts – a swing shift of one month of days and one month of nights. We sometimes worked a shift we called the “pits” because we worked at night all the time and slept almost all of the days. These lasted three months. Some of us formed bowling teams at the end of our morning shifts. In the summer, we had a baseball team and practiced on our half hour lunch time, 15 minutes off in the morning and 15 minutes off in the afternoon.
Because of plant safety rules we wore a head scarf covering all of our hair until “Snoods” were invented. Safety oxfords with hard toes were a must as well as safety glasses. On our job we also wore slacks and blouses with no buttons to catch in our machinery and no jewelry. There were various articles on us featured in the Annual Employee Pullman Magazine of 1943.
My partner from trade school and I were assigned to “Spars”, where we worked on long jigs with a large drill press at each end which we each operated and met in the middle. These were used to make precise holes every so often to hold rivets put in on what they called the “uprights” to finish off the spars. The Spars Department had five or six of these large jigs and we probably put out five per eight hours.
My partner and I took turns doing the riveting and bucking the rivets. When it was our turn to buck the rivet under the jig, we used a small dolly with rollers so we wouldn’t get metal shavings in our butt from the floor. I made the suggestion that everyone use a dolly when bucking rivets to increase speed and save our butts. However, I failed to write the suggestion down and put it in the suggestion box. In the next two days, every jig had a couple of dollies under them and we now became “Dollys on Dollies”. Someone else had turned in my idea and I lost out on a check. After all, what did a gal from a small town know about jigs, rivets, etc. but I learned in a hurry. It was a far cry from beauty school and a fun summer.
I worked for just about three years at Pullman and then came home to join the Navy. After being home for Christmas for the first time in almost three years, I decided to take some time off before finalizing my physical for the Navy. The next thing I knew, the Montgomery Wards Order Office in Cloquet needed a credit manager, so I applied and was hired. It was there that I met a sailor who was home on leave from the South Pacific. He was picking up his mother’s order. It turned out that I had been in kindergarten with him. I finally went out on a date with him, and ended up marrying him three months later, on the base in Washington D.C. (Another interesting story). He was going to school at the Anacostia base, and was going to ship out again after six weeks, so I headed back home to Cloquet. On my way home I stopped in Chicago to visit my sister and was there when the war ended. We all took to the streets, dancing and celebrating. My husband didn’t have to ship out again.
After returning home I helped the Cloquet Red Cross Unit roll bandages, and also helped a friend with records in an office where people applied for food stamps, gas coupons, etc. I enjoyed my time working at the Pullman Aircraft plant as a “Rosie the Riveter” and I would have never given up the experience I received at the Pullman plant, and the contribution I was able to make to support the war.